In the past, small batches of amorphous metals have been produced through a variety of quick-cooling methods. For instance, amorphous metal wires have been produced by sputtering molten metal onto a spinning metal disk (melt spinning). The rapid cooling, on the order of millions of degrees a second, is too fast for crystals to form and the material is "locked in" a glassy state. More recently a number of alloys with critical cooling rates low enough to allow formation of amorphous structure in thick layers (over 1 millimeter) had been produced; these are known as bulk metallic glasses (BMG). Liquidmetal sells a number of titanium-based BMGs, developed in studies originally carried out at Caltech. More recently, batches of amorphous steel have been produced that demonstrate strengths much greater than conventional steel alloys.

An amorphous structure is
The first reported metallic glass was an alloy (Au75Si25) produced at Caltech by W. Klement (Jr.), Willens and Duwez in 1960. This and other early glass-forming alloys had to be cooled extremely rapidly (on the order of one megakelvin per second, 106 K/s) to avoid crystallization. An important consequence of this was that metallic glasses could only be produced in a limited number of forms (typically ribbons, foils, or wires) in which one dimension was small so that heat could be extracted quickly enough to achieve the necessary cooling rate. As a result, metallic glass specimens (with a few exceptions) were limited to thicknesses of less than one hundred micrometers.
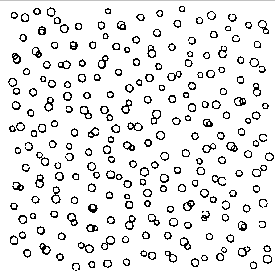
2: The amorphous structure of
In 1969, an alloy of 77.5% palladium, 6% copper, and 16.5% silicon was found to have critical cooling rate between 100 to 1000 K/s.

The amorphous structure of

Amorphous structure of a

network structure of amorphous
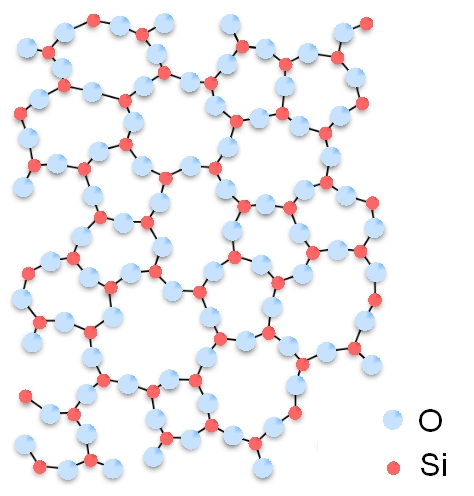
amorphous structures may

An amorphous structure is
The first reported metallic glass was an alloy (Au75Si25) produced at Caltech by W. Klement (Jr.), Willens and Duwez in 1960. This and other early glass-forming alloys had to be cooled extremely rapidly (on the order of one megakelvin per second, 106 K/s) to avoid crystallization. An important consequence of this was that metallic glasses could only be produced in a limited number of forms (typically ribbons, foils, or wires) in which one dimension was small so that heat could be extracted quickly enough to achieve the necessary cooling rate. As a result, metallic glass specimens (with a few exceptions) were limited to thicknesses of less than one hundred micrometers.
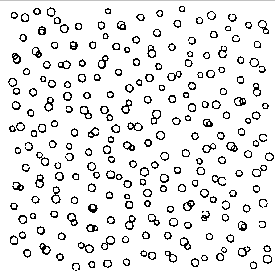
2: The amorphous structure of
In 1969, an alloy of 77.5% palladium, 6% copper, and 16.5% silicon was found to have critical cooling rate between 100 to 1000 K/s.

The amorphous structure of

Amorphous structure of a

network structure of amorphous
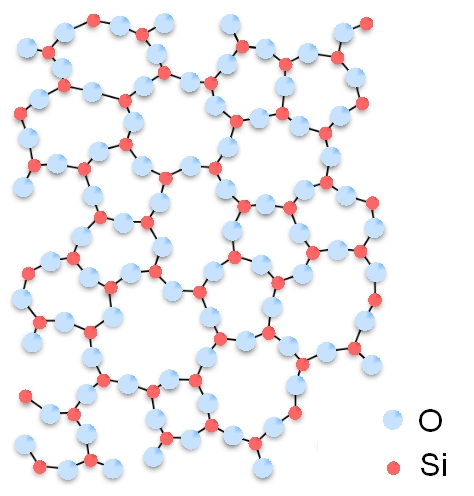
amorphous structures may
No comments:
Post a Comment